Complete 500,000 TPY Wire Rod Block Mill Line
- Design and build as a high-speed wire rod block mill line with an annual output of 500,000 tons. The billet size: 150x150mm, 6-12m.
- Final wire rod size: φ5.5mm—φ16mm, rolling speed: 90m/s – 125m/s,
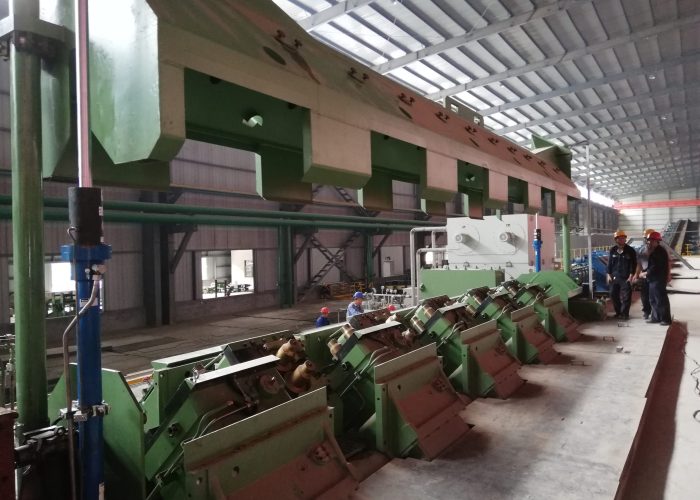
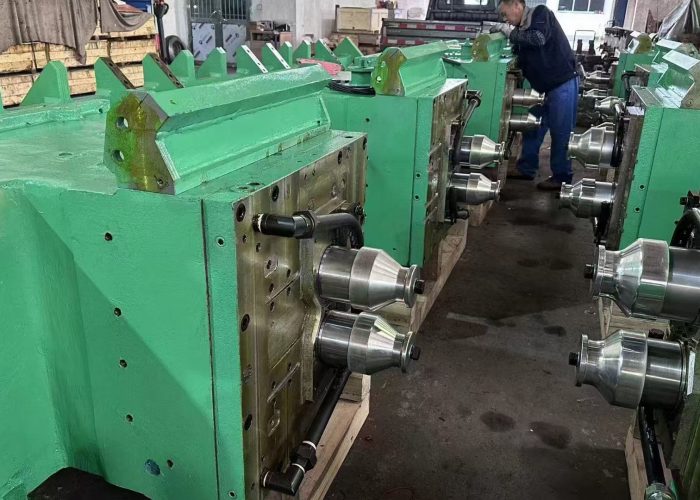

Details Description
- Design and build as a high-speed wire rod mill line with an annual output of 500,000 tons. The billet size: 150x150mm 6-12m.
- Rolling finished product specifications: φ5.5mm—φ16mm, rolling speed: 90m/s – 125m/s.
- Rolled steel grade: Carbon steel, low alloy steel, high alloy steel, high-quality carbon structural steel, etc.
- 28 stands rolling mills are arranged in the whole high-speed wire rod mill line. The roughing rolling mill and intermediate rolling mills are DANIELI (Danieri) short stress path rolling mill models and 16 stands horizontal rolling mill and vertical rolling mill installed alternately. 2 sets pre-finishing mill H-V-H-V arrangement and 10 sets finishing mill are all Morgan models, of which the finishing mill is 45° top cross (φ230×5+φ170×5) wire rod mill.
16 stand roughing rolling mills and intermediate rolling mills are arranged in a single line, and the pre-finishing to the collecting and collecting station is a double-line arrangement. The qualified continuous casting billet is transported to the rolling mill heating furnace by roller conveyor, heated to 1050~1150°C by push-type heating furnace, and is pushed out of the furnace by the tapping machine, and the billet is sent to 8 roughing rolling mills by the tapping roller (φ550 ×6+φ420×2) (one to one) rolling, after 1# flying shear shearing, enter 6 middle rolling mills (φ420×4+φ320×4) (one for one) for rolling, and then enter The φ285×2 pre-finishing mill (Morgan model, flat cantilever structure) enters ten finishing mills after passing 3# flying shears, rolling mills and broken shears (8〞×5+6〞×5) (Using Morgan’s 45-degree top-crossing structure), after water-cooling treatment (3 sections of water cooling and 3 sections of slow cooling), the wire rod enters the collecting and collecting part through the pinch roller, the laying machine, and the loose coil cooling roller, and then enters the PF. The wire rod is conveyed, bundled, unloaded, and weighed and piled up for shipment.
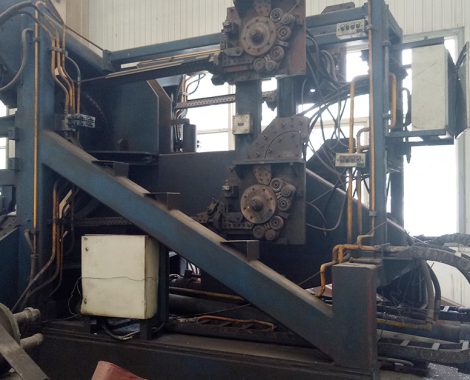
Wire Rod Mill P/F Line System
The P/F line system is important to wire rod mill line. The C hook of P/F line below the coiling station receives the coils from the coiling trolley, completes the cooling, inspection, cutting head and tail, trimming, sampling, pressing and binding, weighing and listing of the coils during the transportation process. Finally, the coiler unloads the coils from the type C hook, and the empty hook returns to the assembly station to continues the next cycle.
Wire Rod Mill Water Cooling System
Wire rod mill water boxes is installed at various locations in a bar or wire rod mill to offer maximum control of the mill temperature profile and therefore control of the mechanical and metallurgical properties. The water box system can be configured for plain carbon products, specialty steel grades, or quench and tempered concrete reinforcement products. Headers are designed to ensure excellent nozzle alignment to minimize the risk of cobbles when changing product sizes.
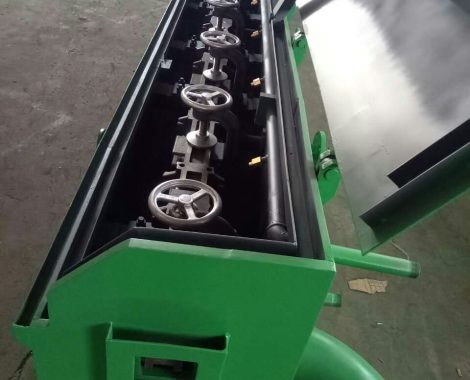
Contact Us
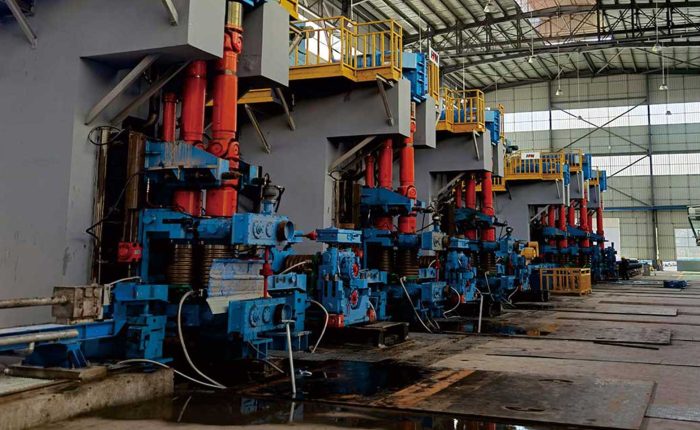