Rolling Mill Roller
- According to product type, rolls can be divided into strip rolls, section rolls, wire rolls.
- According to the position of the rolls in the rolling mill series, there are open rolls, rough rolls, finish rolls.
- According to the roll function, there are broken scale roll, perforated roll, smoothing roll.
- According to the roll material, there are steel roll, cast iron roll, cemented carbide roll, ceramic roll.
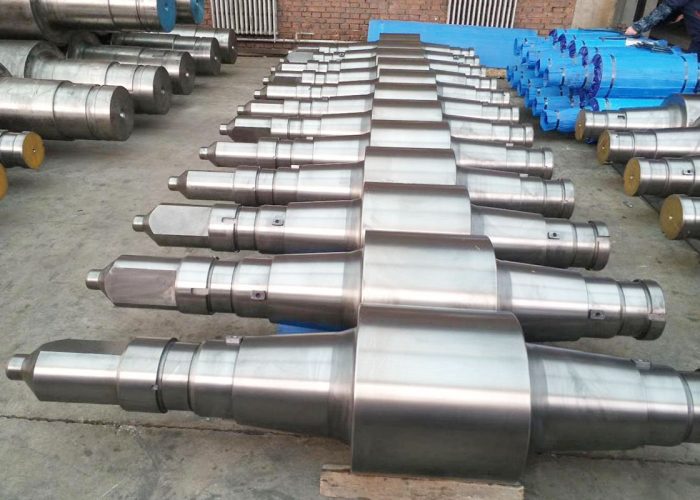
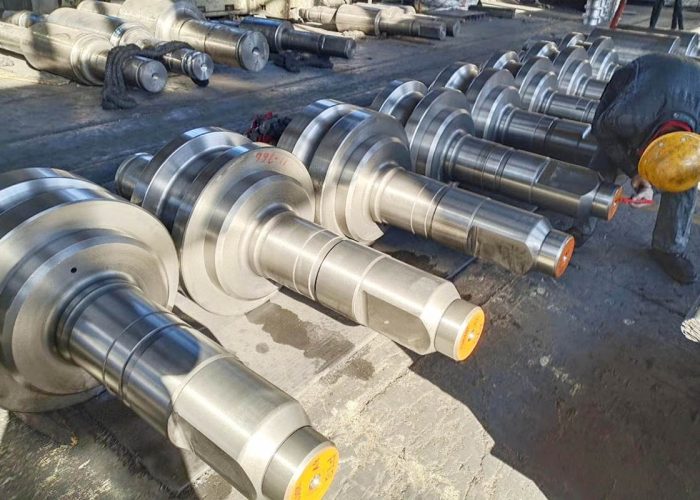

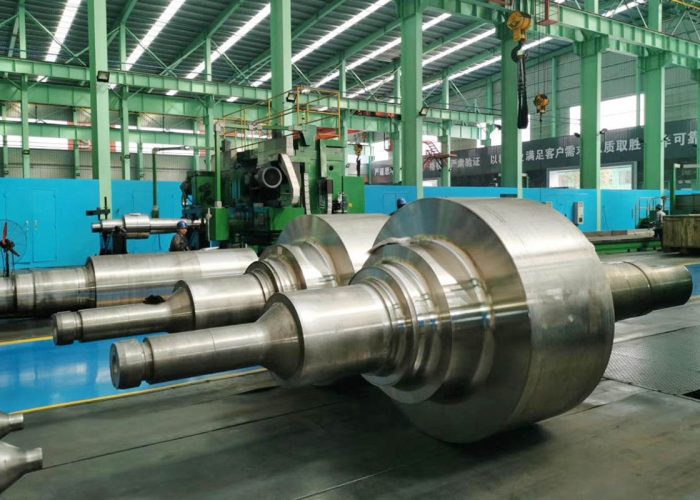
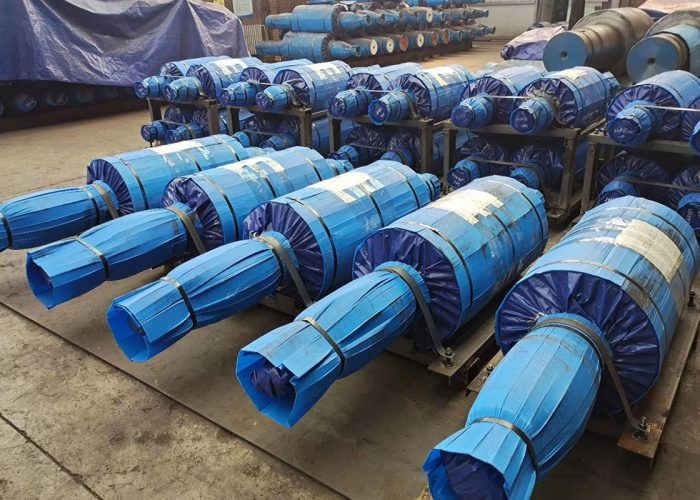
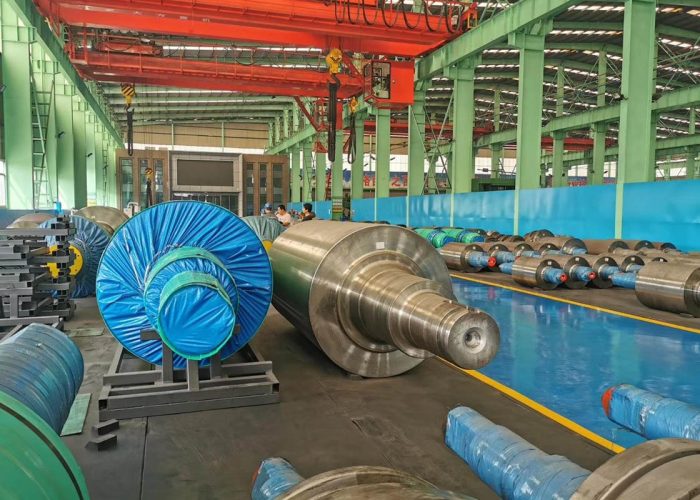
Details Description
Rolling mill roller is the main working part and tools on the rolling mill that cause continuous plastic deformation of the metal. The roll is mainly composed of three parts: roll body, roll neck and shaft head. The rolling mill roller roll body is the middle part of the roll that actually participates in rolling the metal. It has a smooth cylindrical or grooved surface. The roll neck is installed in the bearing, and the rolling force is transmitted to the stand through the bearing seat and the pressing device. The shaft end of the transmission end is connected with the gear seat through the connecting shaft, and transmits the rotating torque of the motor to the roller. The rolls can be arranged in the form of two-roll, three-roll, four-roll or multi-roll in the rolling mill stand.
Parameter:
Roll type | Roll body hardness HS | Roll neck tensile strength/MPa | Main application | |
Cast steel roll | Cast steel Semi-steel Graphite steel High chromium steel Tool steel (high carbon high-speed steel) | 30~70 35~70 35~60 70~80 80~90
| 500~1000 300~700 500~900
| Large and medium-sized steel blank and rough rolling stand, rough rolling stand of strip mill, backup roll; Large, medium and small section steel intermediate and finishing rolling stands, sheet steel work rolls; Large, medium and small section steel rough rolling stand; Strip rough rolling back frame, finish rolling front frame, cold rolled strip steel work roll; Hot rolling strip finishing rolling stand, small or wire rod finishing rolling stand. |
Cast iron roll | Chilled cast iron | 55~85 55~85 35~80 60~95 75~95 | 150~220 150~220 300~700
| Plate, wire, profile, pipe finishing rolling stand; Medium-rolling and finishing rolling stands for sheet, wire, profile, and pipe, and finishing rolling stands for steel strip; Profile, wire, tube thick, medium rolling stand; Small steel and wire rod mill finishing rolling stand, strip pre-finishing rolling stand; Pre-finish rolling of small size, wire rod and tube, finish rolling. |
Powder metallurgy roll | Tungsten carbide Tool steel | 80~90 80~90
| Small, wire rod finishing rolling stand, cold rolled steel; Small, wire rod finishing stand, strip steel finishing stand. | |
Forged steel roll | Hot roll Cold roll Backup roll Forged semi-steel and white iron | 35~60 75~105 40~70 35~70 | 500~1100 700~1400 700~1400 500~1000 | Open billet, large rough rolling stand, sheet steel rough rolling stand; Cold-rolled steel work roll, profile, welded tube forming roll; Cold and hot strip mill; Large, medium and small. |
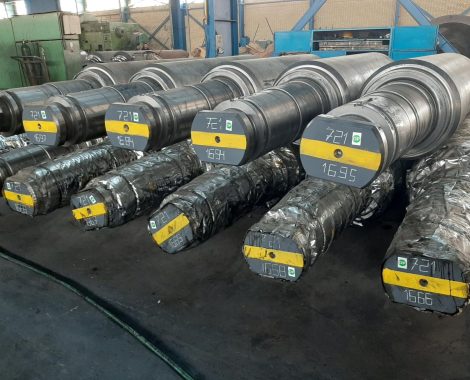
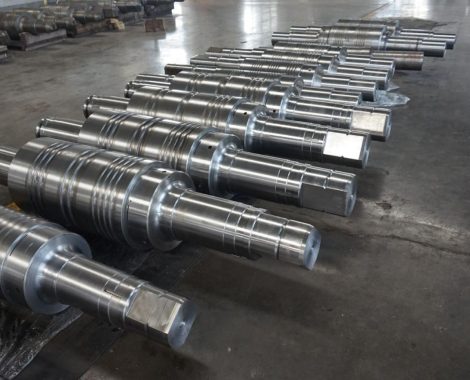
Working conditions of hot rolls
(1) The hot roll material must have high hardenability. (2) The hot roll must have a low coefficient of thermal expansion. (3) The hot roll must have high thermal conductivity and high-temperature yield strength. (4) The hot roll must have high oxidation resistance and high temperature creep strength. (5) The hot roll should have excellent tempering resistance and uniform surface hardness, etc.
Working conditions of cold rolls
(1) The roller surface must have a high and uniform surface hardness, usually the hardness should be greater than 62HRC. (2) A deep hardened layer is required, and the hardness of the roller edge must be relatively low. (3) The roller neck has a lower hardness. (4) Cold rolls must have sufficient resistance to cracking and spalling caused by torsional stress, bending stress and shear stress.
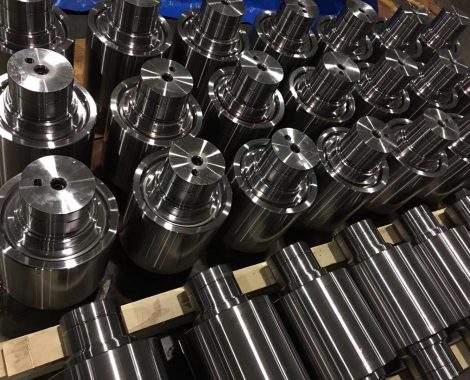
Contact Us
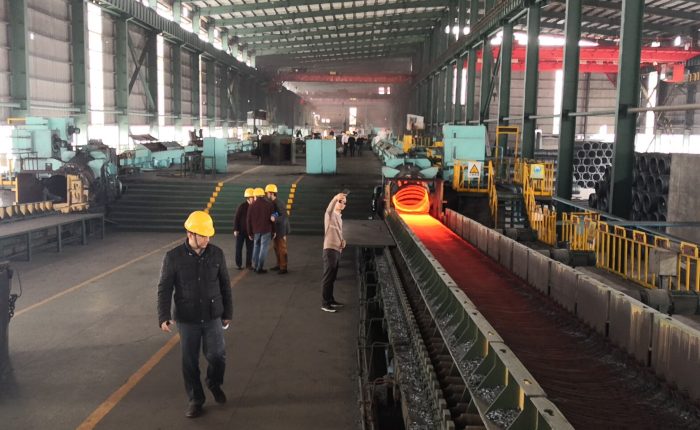